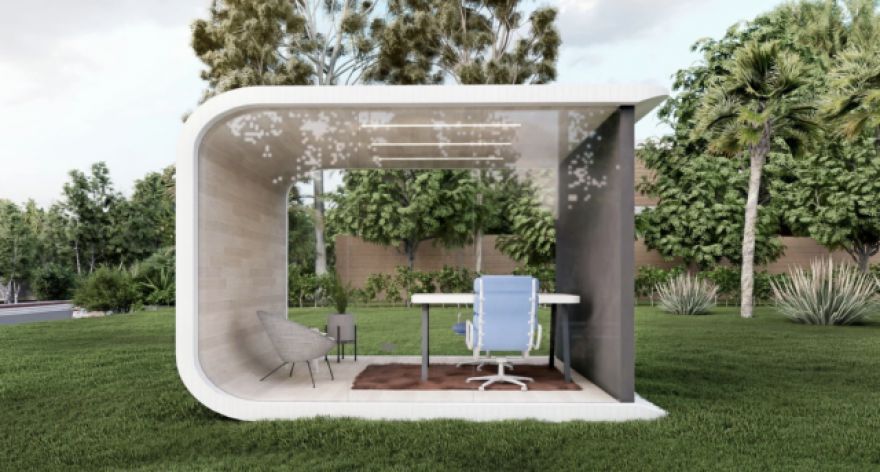
Startup Makes 3D Printed Tiny Homes From Recycled Materials
Los Angeles-based Azure specializes in accessory dwelling units, or ADUs, which typically sit next to or behind a main residence on the same lot. Its designs are highly modern: glass walls, recessed lighting, and pocket doors give each unit a penthouse vibe despite sitting in another home’s backyard. But the company’s aesthetic choices aren’t what command attention. It’s the way in which its units are built.
Azure uses a large 3D printer to produce each unit’s structural skeleton, exterior sheathing, water control barrier, exterior finish, utility passageways, and the grounding for interior finishes.
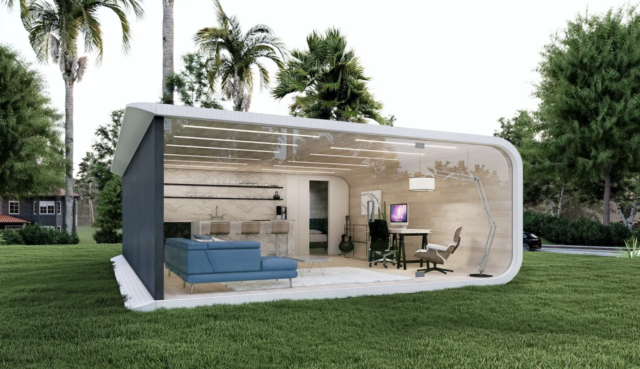
(Photo: Azure)
Whether Azure’s units can be considered affordable really depends on the nuances of one’s personal situation. A 120-square foot, one-room backyard studio starts at $24,900, while a 180-square foot ADU (with its own bathroom and kitchenette) starts at $39,900. The ADU floor plans are quite varied, with two-bedroom units running just under $200,000. In a way, these are good prices—residences at this price point are difficult to find in the US these days, at least without sacrificing aesthetics or quality. Unlike buying a traditional home, however, these units don’t have baked-in land to sit on. Customers need to have a place to plop their unit, and whether financially or by convincing a family member to give up part of their lot, that’s easier said than done.
3D printed homes aren’t entirely new. Last year Habitat for Humanity its first-ever 3D printed house, a 1,200-square foot residence in Virginia, to a single mother and her 13-year-old son. (The home even came with its own 3D printer, in case the family ever needed to replace any of the original structure’s elements.) Just a few months earlier, Florida permitted its for residential use. Still, Azure could become a trendsetter when it comes to the materials used in this modern and efficient building technique.
Now Read: